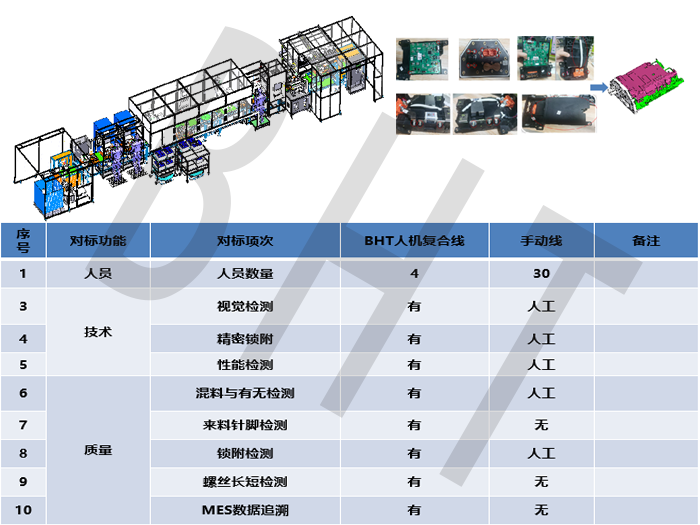
Automatic BDU Assembly-Test line
The automatic BDU assembly testing line is used for the assembly and testing production line of automotive engine assembly control modules.
The entire line is divided into three main parts (PCBA substrate inspection section, shell&PCBA assembly section, and product testing and cutting section):
The first part covers (PCBA substrate inspection section): PCBA board automatic feeding, 2D AOI inspection, 3D AOI inspection, ICT testing, substrate burning, and semi functional testing;
The second part covers (shell&PCBA assembly section): upper shell and PCBA gluing assembly, lower shell laser engraving assembly, hook bending assembly, air tightness testing, and product static placement.
The third part covers (product testing and cutting section): high load testing, high temperature aging, functional testing, vehicle program updates, installation of ventilation valves, finished product barcode printing, PIN needle detection, product cutting, and box labeling.
The entire line is divided into three main parts (PCBA substrate inspection section, shell&PCBA assembly section, and product testing and cutting section):
The first part covers (PCBA substrate inspection section): PCBA board automatic feeding, 2D AOI inspection, 3D AOI inspection, ICT testing, substrate burning, and semi functional testing;
The second part covers (shell&PCBA assembly section): upper shell and PCBA gluing assembly, lower shell laser engraving assembly, hook bending assembly, air tightness testing, and product static placement.
The third part covers (product testing and cutting section): high load testing, high temperature aging, functional testing, vehicle program updates, installation of ventilation valves, finished product barcode printing, PIN needle detection, product cutting, and box labeling.
Product application areas
This equipment is used for the assembly and testing production line of automotive engine assembly control modules.
The entire line is divided into three main parts (PCBA substrate inspection section, shell&PCBA assembly section, and product testing and cutting section):
The first part covers (PCBA substrate inspection section): PCBA board automatic feeding, 2D AOI inspection, 3D AOI inspection, ICT testing, substrate burning, and semi functional testing;
The second part covers (shell&PCBA assembly section): upper shell and PCBA gluing assembly, lower shell laser engraving assembly, hook bending assembly, air tightness testing, and product static placement.
The third part covers (product testing and cutting section): high load testing, high temperature aging, functional testing, vehicle program updates, installation of ventilation valves, finished product barcode printing, PIN needle detection, product cutting, and box labeling.
parameter
Capacity: 40PCS/H (monthly capacity can reach 24000 pcs/month/double shift)
Yield rate: 99.9%
Applicable products: 112PIN and 196PIN
The entire line is divided into three main parts (PCBA substrate inspection section, shell&PCBA assembly section, and product testing and cutting section):
The first part covers (PCBA substrate inspection section): PCBA board automatic feeding, 2D AOI inspection, 3D AOI inspection, ICT testing, substrate burning, and semi functional testing;
The second part covers (shell&PCBA assembly section): upper shell and PCBA gluing assembly, lower shell laser engraving assembly, hook bending assembly, air tightness testing, and product static placement.
The third part covers (product testing and cutting section): high load testing, high temperature aging, functional testing, vehicle program updates, installation of ventilation valves, finished product barcode printing, PIN needle detection, product cutting, and box labeling.
parameter
Capacity: 40PCS/H (monthly capacity can reach 24000 pcs/month/double shift)
Yield rate: 99.9%
Applicable products: 112PIN and 196PIN
Related product
-
Automatic BDU Assembly-Test lineDetail