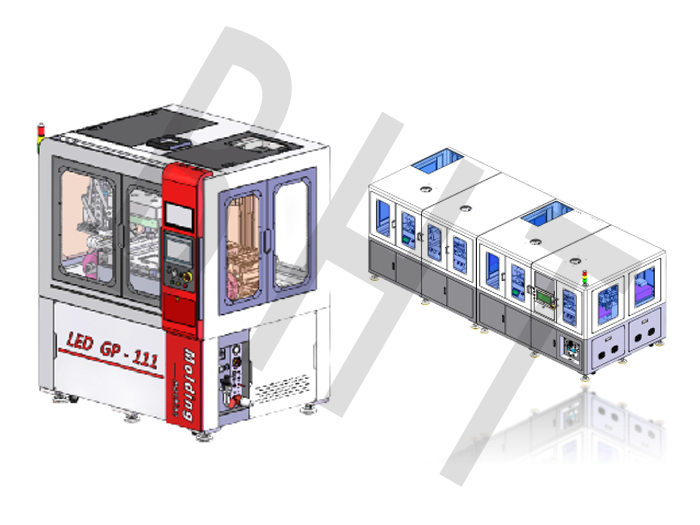
INTELLIGENT EQUIPMENT - MOLDING MACHINE
brief introduction
The fully automatic molding machine belongs to the semiconductor packaging equipment, which is applied in the film pressing process of MIP lamp beads and modules in the MiniLED process, and can also be used in the chip plastic packaging process. Using release film assisted packaging, the packaging adhesive is flattened and cured on the surface of the substrate or module to form a protective film, which provides waterproof, dustproof, and anti-collision protection for components such as chips and light beads. Our company has successfully developed various models such as one to one, one to two, and one to four, which can operate independently or be produced online.
The fully automatic molding machine belongs to the semiconductor packaging equipment, which is applied in the film pressing process of MIP lamp beads and modules in the MiniLED process, and can also be used in the chip plastic packaging process. Using release film assisted packaging, the packaging adhesive is flattened and cured on the surface of the substrate or module to form a protective film, which provides waterproof, dustproof, and anti-collision protection for components such as chips and light beads. Our company has successfully developed various models such as one to one, one to two, and one to four, which can operate independently or be produced online.
Product application areas
Core Technology:
Mold clamping pressure and stroke control: uniform heating and temperature control of the mold
Multi channel vacuum exhaust system for mold cavity: adjustment of molding process parameters
Visual positioning algorithm software and six axis robotic arm motion control
Key parameters:
Equipment production capacity: UPH ≥ 12PCS/H per output; One out two UPH ≥ 24PCS/H and one out four UPH ≥ 40PCS/H (depending on the specific product process)
Yield rate: ≥ 99.8%
Product size: MAX L190xW330xmm (customizable)
Film pressure thickness: (0.2~0.6) ± 0.015mm
Equipment size: L1700xW1300xH2000mm
Mold clamping pressure and stroke control: uniform heating and temperature control of the mold
Multi channel vacuum exhaust system for mold cavity: adjustment of molding process parameters
Visual positioning algorithm software and six axis robotic arm motion control
Key parameters:
Equipment production capacity: UPH ≥ 12PCS/H per output; One out two UPH ≥ 24PCS/H and one out four UPH ≥ 40PCS/H (depending on the specific product process)
Yield rate: ≥ 99.8%
Product size: MAX L190xW330xmm (customizable)
Film pressure thickness: (0.2~0.6) ± 0.015mm
Equipment size: L1700xW1300xH2000mm